By: Jim Marotta; Originally posted on blog.gale.com
Ford introduced 4-wheel air suspension (4WAS) in 1995 and has since made it available on all three generations of the Ford Expedition and Lincoln Navigator.System components:
- The electric air compressor mounts behind the right headlight and includes a built-in vent solenoid valve and a replaceable air dryer.
- A solenoid valve at each suspension unit.
- The front and rear fill solenoids isolate the front/rear air shocks from the rest of the system.
- The front gate solenoid isolates the front air shocks from each other, so the pressure between them does not equalize as the vehicle rolls in a turn.
- A pressure relief valve is mounted on the frame crossmember near the rear height sensor.
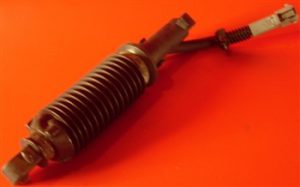
- On 2006 and earlier models, there are two linear ride height sensors, one mounted between the rear suspension panhard rod and the crossmember just forward of the spare tire, and one between the frame and the left front upper control arm.
- Later models have four identical potentiometer-type sensors, one at each corner, permanently mounted to left- and right-side brackets, which are bolted to the frame, and a small ball stud link connects the sensor arm to the suspension arm.
- On earlier models, a single control unit is used for the 4WAS, the rear air suspension system and the EVO steering control module. On later models, air suspension is controlled by the vehicle dynamics module, mounted above the parking brake handle.
- On 1997-02 models, a manual air suspension switch behind the front passenger side kick panel turns the system off for service or long-term storage. On newer models, it’s behind an access panel aft of the third-row seat on the driver side.
- Two nylon air lines connect directly to the drier mounted on the compressor, one leading to the front fill solenoid valve and the other to the rear fill valve. Quick-connect fittings are used throughout the system. The air lines cannot be repaired or spliced.
- When the ignition switch is first turned ON, the control runs a self-diagnostic test. If a malfunction is detected, the system will default to trim height, either by operating the compressor or by venting pressure as needed.
- Turn the manual air suspension switch off any time the wheels are lifted off the ground. Failure to do so can cause expensive damage, especially to the rear air springs.
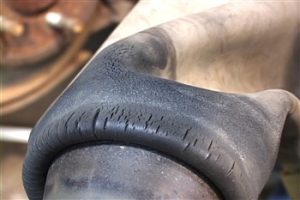
- The only service required by the 4WAS itself is a visual inspection. Look for physical damage to the air springs, cut or crimped air lines, or evidence of something rubbing the lines. There is no pressure sensor in the system. Symptoms of a leak include excessive compressor operation, failure to reach or maintain commanded height, and most commonly, a sagging rear end.
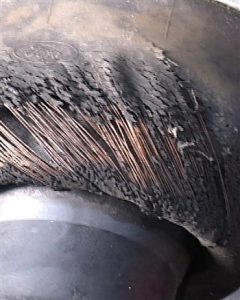
- Use soapy water to leak-check fittings, check the whole system with a smoke machine. Do not, under any circumstances, disconnect any fittings without venting the system first.
- Check height sensors for damage and to make sure they’re securely mounted. With the vehicle at trim height, sensor output should be 2.66 volts. Using ChiltonLibrary, consult the wiring diagrams for the correct pin locations to measure the voltage.

- Historically the most troublesome part of the system is the compressor. Failures tend to be gradual rather than catastrophic. When replacing a compressor, techs often replace the solid-state relay too.